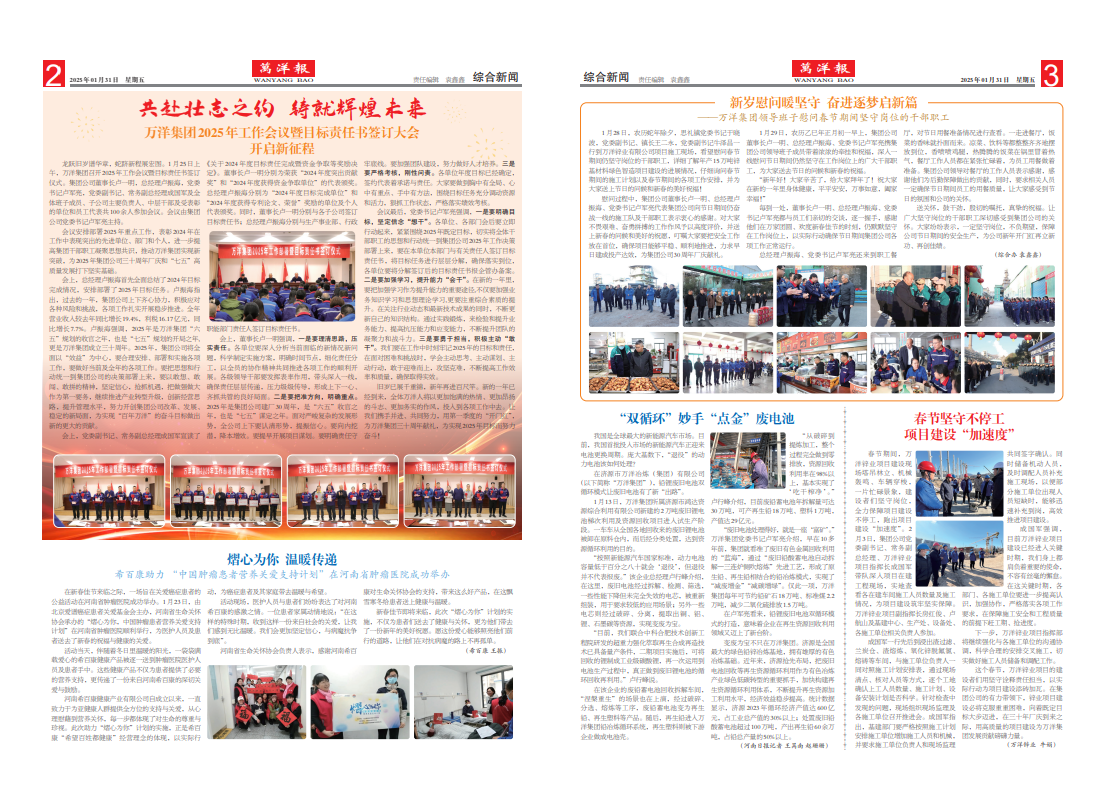
“双循环”妙手“点金”废电池
我国是全球最大的新能源汽车市场。目前,我国首批投入市场的新能源汽车正迎来电池更换周期。庞大基数下,“退役”的动力电池该如何处理?
在济源市万洋冶炼(集团)有限公司(以下简称“万洋集团”),铅锂废旧电池双循环模式让废旧电池有了新“出路”。
1月13日,万洋集团所属济源市鸿达资源综合利用有限公司新建的2万吨废旧锂电池梯次利用及资源回收项目进入试生产阶段。一车车从全国各地回收来的废旧锂电池被卸在原料仓内,而后经分类处置,达到资源循环利用的目的。
“按照新能源汽车国家标准,动力电池容量低于百分之八十就会‘退役’,但退役并不代表报废。”该企业总经理卢行峰介绍,在这里,废旧电池经过拆解、检测、筛选,一些性能下降但未完全失效的电芯,被重新组装,用于要求较低的应用场景;另外一些电芯则经过破碎、分离,提取出铜、铝、锂、石墨碳等资源,实现变废为宝。
“目前,我们联合中科合肥技术创新工程院研发的超重力强化萃取再生合成再造技术已具备量产条件,二期项目实施后,可将回收的锂制成工业级碳酸锂,再一次运用到电池生产过程中,真正做到废旧锂电池的循环回收再利用。”卢行峰说。
在该企业的废铅蓄电池回收拆解车间,“涅槃重生”的场景也在上演,经过破碎、分选、熔炼等工序,废铅蓄电池变为再生铅、再生塑料等产品。随后,再生铅进入万洋集团铅冶炼循环系统,再生塑料则被下游企业做成电池壳。
“从破碎到提炼加工,整个过程完全做到零排放,资源回收利用率在98%以上,基本实现了‘吃干榨净’。”卢行峰介绍,目前废铅蓄电池年拆解量可达30万吨,可产再生铅18万吨、塑料1万吨,产值达29亿元。
“废旧电池处理得好,就是一座‘富矿’。”万洋集团党委书记卢军亮介绍,早在10多年前,集团就看准了废旧有色金属回收利用的“蓝海”,通过“废旧铅酸蓄电池自动拆解—三连炉侧吹熔炼”先进工艺,形成了原生铅、再生铅相结合的铅冶炼模式,实现了“减废增金”“减碳增绿”。仅此一项,万洋集团每年可节约铅矿石18万吨、标准煤2.2万吨,减少二氧化硫排放1.5万吨。
在卢军亮看来,铅锂废旧电池双循环模式的打造,意味着企业在再生资源回收利用领域又迈上了新台阶。
变废为宝不只在万洋集团。济源是全国最大的绿色铅锌冶炼基地,拥有雄厚的有色冶炼基础。近年来,济源抢先布局,把废旧电池回收等再生资源循环利用作为有色冶炼产业绿色低碳转型的重要抓手,加快构建再生资源循环利用体系,不断提升再生资源加工利用水平,经济效益稳步提高。统计数据显示,济源2023年循环经济产值达600亿元,占工业总产值的30%以上;处置废旧铅酸蓄电池超过100万吨,产出再生铅60余万吨,占铅总产量的50%以上。